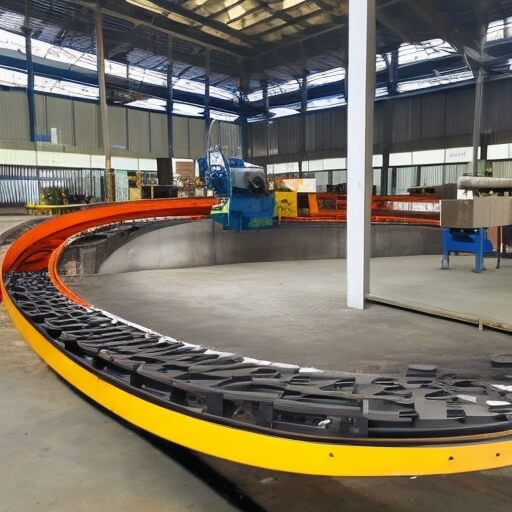
Conveyor Systems: Streamlining Fabrication and Welding Processes
In the fast-paced world of fabrication and welding, efficiency is key. One crucial element for achieving maximum productivity is the use of well-designed conveyor systems. These automated pathways move materials throughout the production process, minimizing manual handling and expediting workflows. This guide explores the benefits of using conveyors in fabrication and welding, along with the various types available to suit your specific needs.
Benefits of Conveyor Systems in Fabrication and Welding:
- Increased Productivity: Automated material movement frees up workers for more skilled tasks, boosting overall output.
- Reduced Labor Costs: By minimizing manual handling, conveyor systems lower reliance on manpower, leading to cost savings.
- Improved Safety: Automation reduces the risk of injuries associated with manual material handling, creating a safer work environment.
- Enhanced Quality Control: Consistent and controlled material movement minimizes damage and allows for better quality control.
- Reduced Lead Times: Faster workflows translate to quicker production cycles and faster delivery times.
Choosing the Right Conveyor for Your Needs:
With a wide variety of conveyor types available, selecting the best fit for your application is crucial. Here are some common options:
1. Belt Conveyors: These versatile systems employ a continuous belt to move materials across flat or inclined surfaces. Ideal for transporting various shapes and sizes.
2. Roller Conveyors: Featuring rows of rollers, these conveyors excel at moving lighter materials and irregularly shaped objects. Often used in assembly lines and workstations.
3. Overhead Conveyors: Suspended from the ceiling, these systems offer unobstructed floor space and are perfect for heavy or bulky materials.
4. Chain Conveyors: These robust systems utilize chains to pull or push materials, ideal for demanding applications and steep inclines.
5. Powered Roller Conveyors: Equipped with individual motors on each roller, these conveyors allow for variable speed control and precise positioning of materials.
6. Accumulation Conveyors: Designed to hold items temporarily without stopping the flow, these systems are ideal for buffering materials between processes.
7. Vertical Conveyors: These specialized systems transport materials vertically, efficiently utilizing floor space and saving horizontal travel time.
Additional factors to consider when choosing a conveyor:
- Material type and weight
- Conveyor speed and capacity
- Layout and space constraints
- Budget and required features
By carefully considering your specific needs and the available options, you can select a conveyor system that optimizes your fabrication and welding operations, boosting efficiency, safety, and profitability.
Conveyor systems are powerful tools for enhancing the efficiency and productivity of fabrication and welding processes. With a wide range of types available, there’s a perfect solution for every application. By investing in the right conveyor system, you can streamline your operations, reduce costs, and achieve higher-quality results.